Corrugated Iron Sheet Making Machine
Corrugated sheet roll forming machines are used to produce corrugated roof and wall panels in construction, housing, manufacturing, industry, warehouses, and factories.

The raw materials used to manufacture corrugated metal roofs and wall panels are various metals and galvanized steel coils, such as copper, aluminum, zinc alloys, and stainless steel. The most commonly used and cost-effective raw materials for corrugated roof sheet roll forming machines include pre-coated steel, galvanized steel, and aluminum zinc steel.
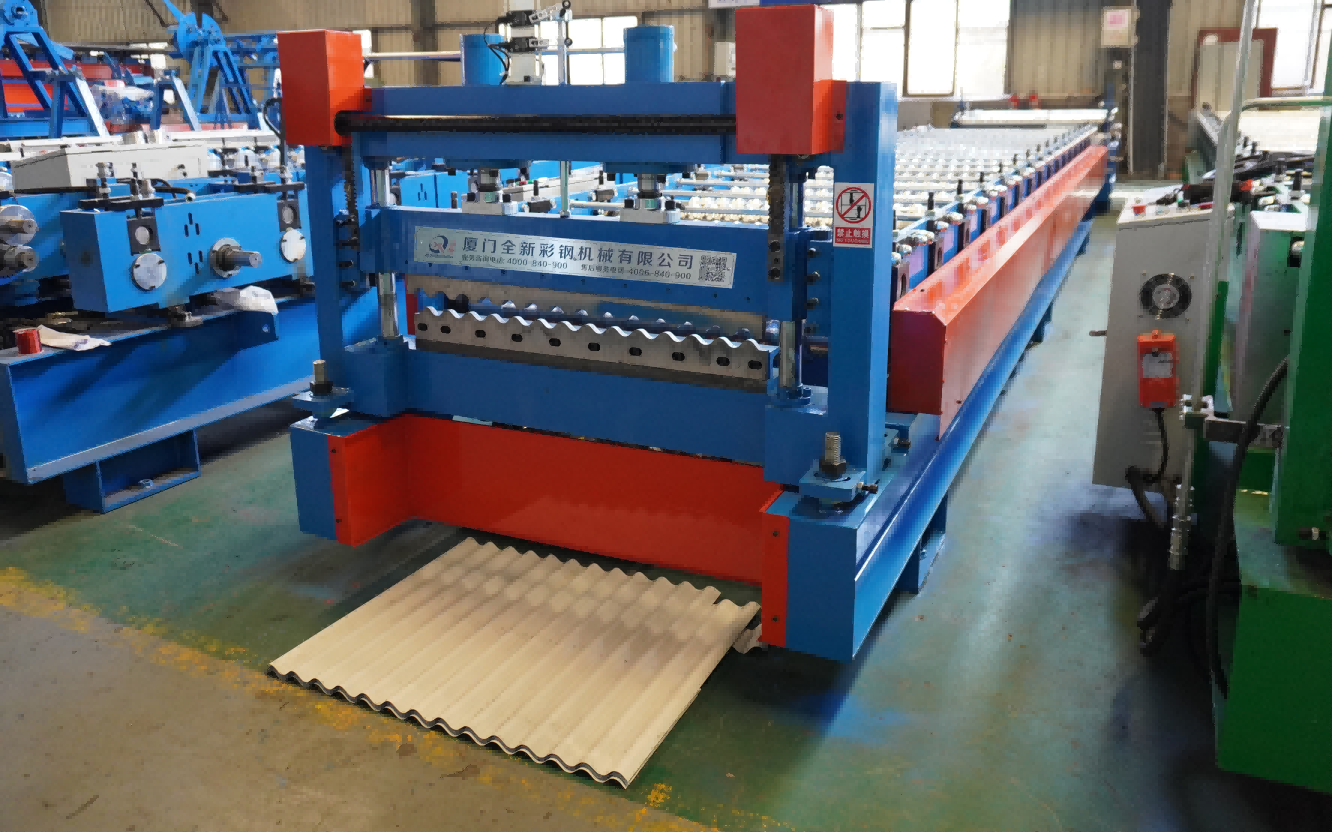
In the African market, corrugated roof sheet roll forming machines and IBR sheet roll forming machines have become two popular products in metal sheet roll forming equipment. Among them, corrugated roof sheet roll forming machines play an important role in the field of metal roof and wall panel manufacturing with their excellent performance.
The equipment routinely processes materials with a thickness range of 0.3 – 0.8 mm and a width between 914 – 1250 mm, which can meet diverse production needs. The most popular roll-forming machine for corrugated iron roof and siding panels on the market is capable of producing roof panels with sinusoidal corrugations in effective widths of 762 mm, 838 mm and 1080 mm, with a fixed wave pitch of 76.2 mm and a wave height of 18 mm. It is particularly worth mentioning that the same machine can produce panels of different effective widths, which greatly improves the practicality and production efficiency of the equipment and saves equipment costs and production space for manufacturers.

The corrugated sheet roll-forming machine integrates multiple key components to provide a full range of solutions for the efficient production of corrugated sheets. In the raw material input link, it is equipped with a manual unwinder, and users can also upgrade it to a hydraulic unwinder with a load capacity of 5 tons according to their needs to meet the production needs of different scales. Connected to it is the inlet feed guide, which can be flexibly adjusted to adapt to materials of various widths, greatly improving the versatility of the equipment.
The roll-forming system is the core of the entire equipment, responsible for accurately processing metal sheets into corrugated shapes. The transmission system is like the “power hub” of the equipment, ensuring the smooth operation of the production line and ensuring close cooperation between all links.
In terms of power and control, the hydraulic system provides strong power support and provides solid guarantee for the stable operation of the equipment. As the power source of the hydraulic system, the oil pump continuously delivers power. The control system monitors and accurately adjusts various operating parameters in real time to ensure the accuracy and stability of the production process.
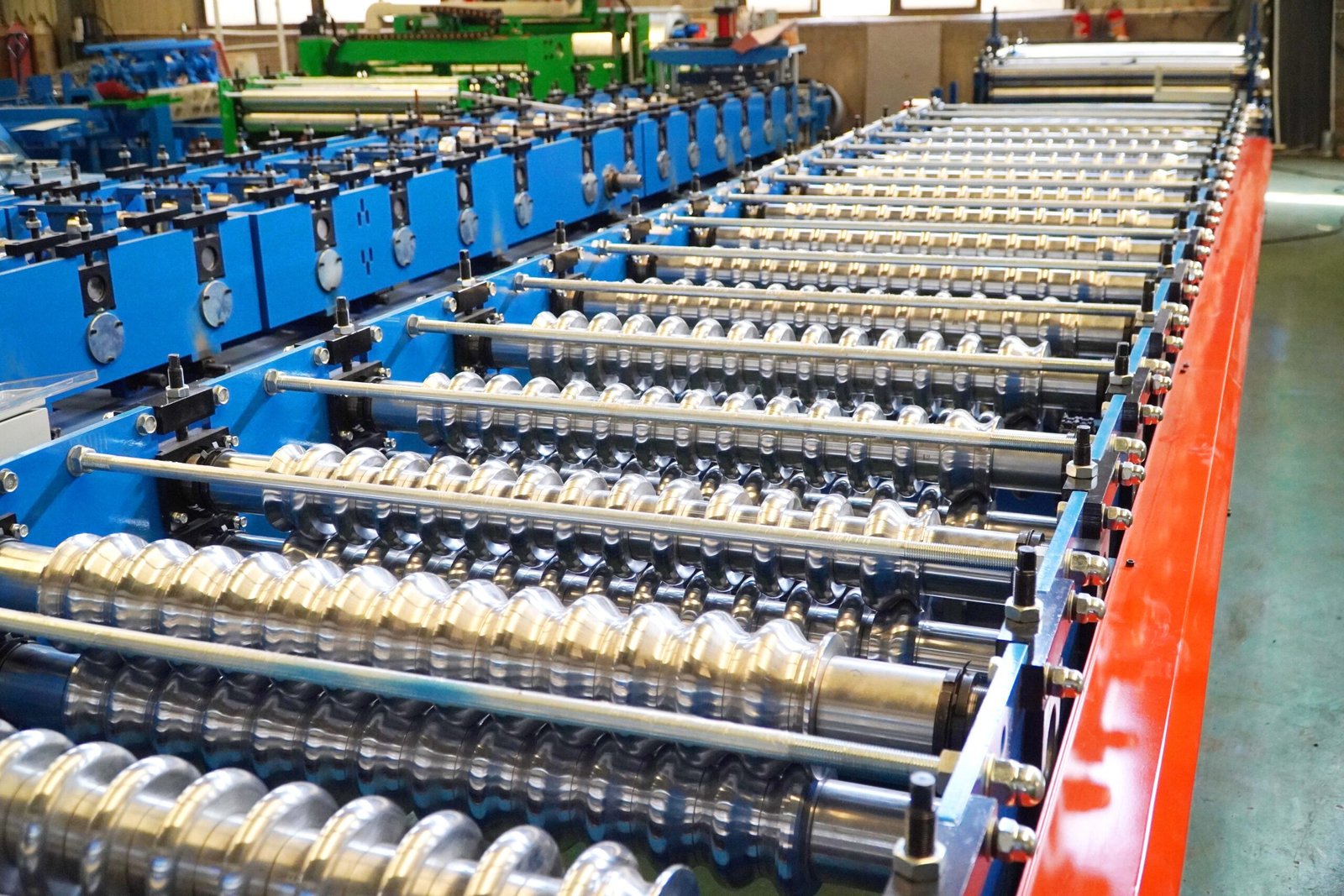
In the finished product processing link, the hydraulic cutting machine can achieve high-precision plate cutting to ensure the accuracy of the finished product size. The output table is used to store the finished products for subsequent handling and sorting.
For the European market, the equipment has also been specially optimized, with a safety cover and a CE mark to ensure full compliance with the strict local safety standards and regulatory requirements in Europe, and to protect the promotion and use of the product in the European market.
This corrugated sheet roll forming machine is specially built for South African customers, and its main purpose is to produce corrugated roof panels. It is worth mentioning that all iron corrugated roof panel manufacturing machines have customized characteristics and can be adjusted according to the needs of specific application scenarios. After all, different applications have different requirements for corrugated sheets. For example, for steel silo corrugated sheet roll forming machines, the corrugated sidewalls of commercial storage silos usually require 2mm thick materials, while the thickness of some silo corrugated sheets is as high as 8mm. Therefore, if you need a corrugated sheet forming machine for a specific application, providing technical drawings of corrugated sheets is an essential step.
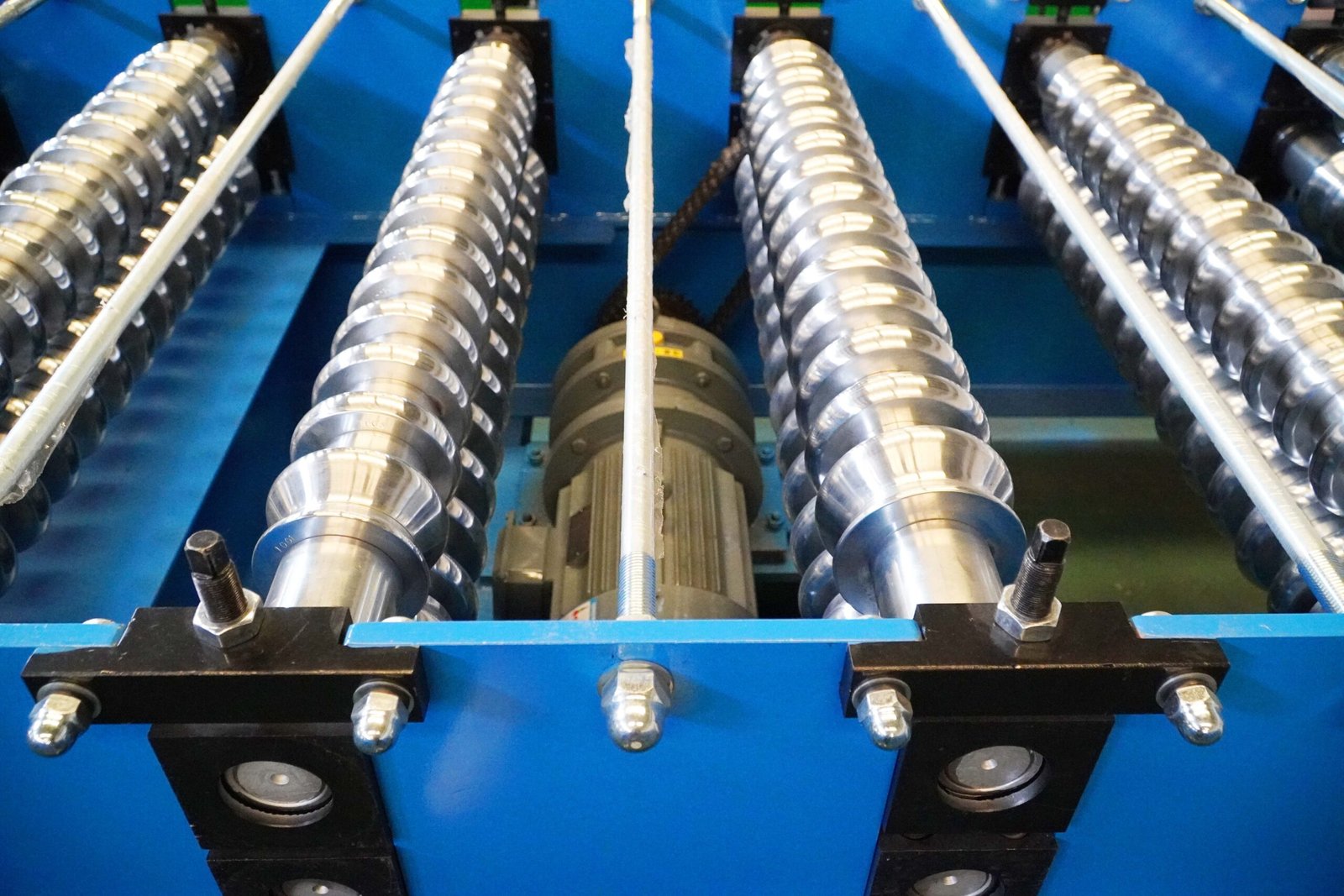
Raw material related parameters
Types: pre-coated color steel coils, galvanized steel coils, aluminum-zinc coated steel coils.
Yield strength: 235MPA – 550MPA.
Thickness: 0.3 – 0.8mm.
Width: 914 – 1250mm.
Main equipment parameters
Main motor power: 5.5 KW.
Forming stations: 16 – 22 stations.
Structure related
Rolling mill frame structure: one-piece or split.
Forming tool structure frame: welded structural steel, steel thickness 18mm.
Roller and shaft
Roller material: high quality 45# steel, polished and plated with 0.05mm chrome.
Shaft material: high quality 45# steel, shaft diameter 70mm.
Cutter part
Cutter type: hydraulic cutter and stop cutting.
Cutter mold material: Cr12 steel.
Cutting hydraulic power: 4KW.
Cutting length and quantity: The final sinusoidal corrugated roof panels can be automatically cut according to the required length and quantity, and the customer sets the quantity through the touch screen on the PLC control box.
Control system
Adopts Panasonic PLC, inverter, CHNT transformer and Omron encoder.
If you have other ideas about the expression style, degree of detail, etc. of the content, such as wanting a more colloquial introduction, please let me know.
Application
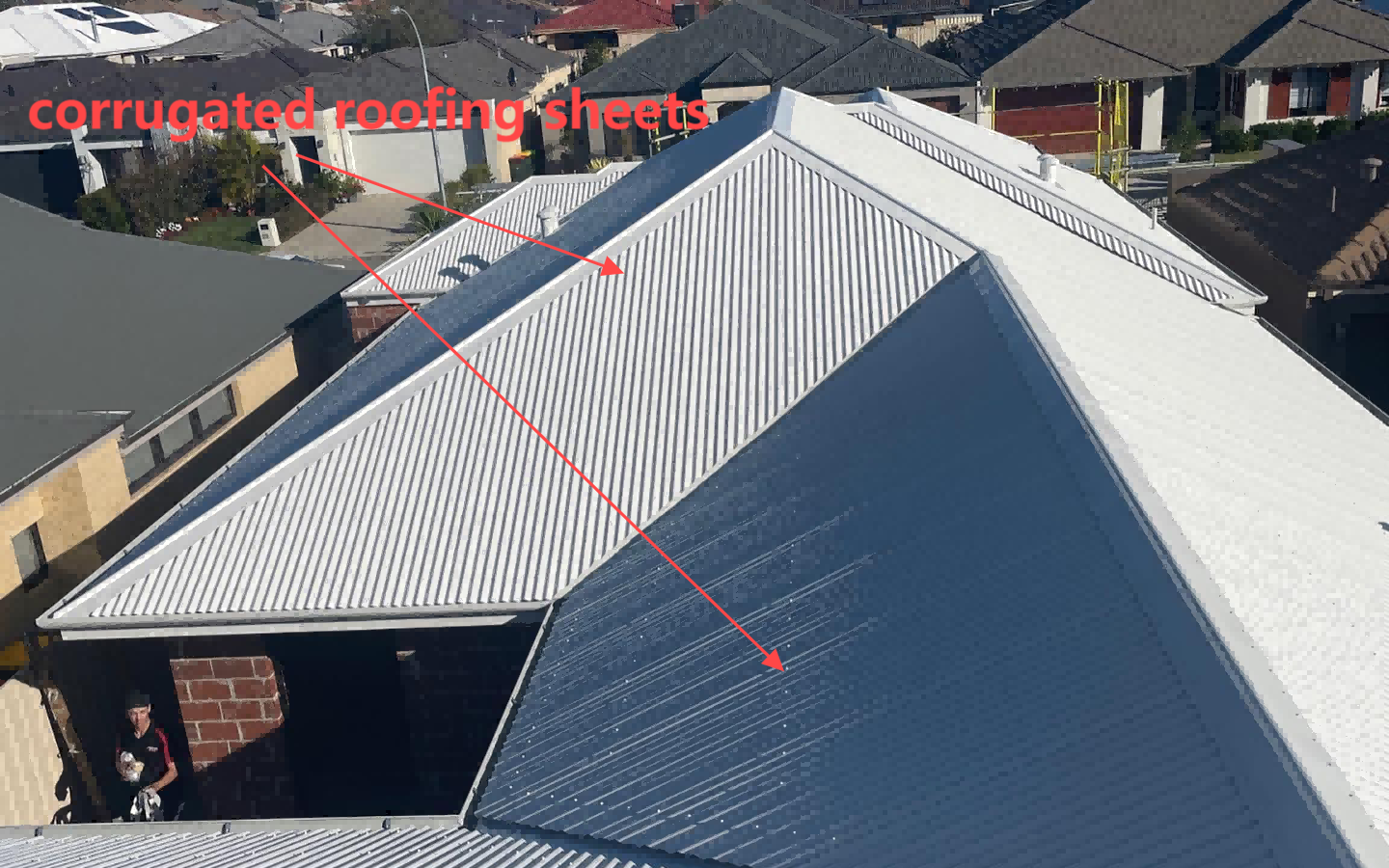
Machine Features
The manufacturing of corrugated metal roofs and wall panels is supported by a wide array of raw materials. These predominantly consist of various metals and galvanized steel coils, including copper, aluminum, zinc alloy, and stainless steel. Each of these materials, owing to their unique properties, finds extensive application in diverse demand scenarios. However, when it comes to the practical production with corrugated roof sheet roll forming machines, pre – coated steel, galvanized steel, and aluminum – zinc steel are the most prevalently utilized raw materials considering cost – effectiveness.
Pre – coated steel stands out with its excellent corrosion resistance and aesthetic appeal. The surface coating effectively shields it from environmental degradation. Additionally, it offers a wide spectrum of colors, catering to the aesthetic requirements of different buildings. Galvanized steel, with its well – established galvanizing process, provides outstanding rust resistance while keeping costs under control. Aluminum – zinc steel, on the other hand, combines the merits of aluminum and zinc. It not only exhibits robust corrosion resistance but also demonstrates remarkable processing capabilities. These three materials strike an ideal balance between cost and quality, making them top choices.
1. Tailored Solutions for Diverse Requirements
We are acutely aware that the demands for corrugated sheet production vary significantly among different customers. Hence, we are well – equipped to offer a plethora of corrugated sheet roll forming line combinations based on customers’ specific needs. Whether it’s production speed, capacity range, or working thickness, we can customize a solution that precisely aligns with your individualized production requirements.
2. Energy – Efficiency: Pioneering High – Performance, Low – Consumption Production
Leveraging advanced technology and meticulously designed corrugated roller forming machine production lines, we are able to achieve substantial energy savings without compromising on product quality. In comparison to market competitors, our products can produce the same quantity of corrugated boards with minimal energy consumption. This not only cuts down on your production costs but also enhances overall production efficiency.
3. User – Friendly Operation for Hassle – Free Start – up
Our corrugated metal roofing machines feature a simple and intuitive control system. The work adjustment mechanism is straightforward, enabling even novice operators to quickly get up to speed. With easy operation, you can ensure a smooth and efficient production process, minimizing the time and labor costs associated with complex operations.
4. Versatile Combinations for Optimal Production Adaptability
For the diverse parameters involved in corrugated board production, such as different thickness ranges and stacking lengths, we present multiple alternative machine combination solutions. This flexibility allows you to select the most suitable configuration according to your actual production needs, guaranteeing both production efficiency and stability.
5. Precision Production Rooted in Extensive Experience
Benefiting from our vast experience in the corrugated paper rolling machine production field, we have an in – depth understanding of customers’ operational requirements. We are committed to providing professional alternative solutions. By sharing our expertise with you, we can accurately match the most suitable corrugated paper rolling machine to your specific needs, ensuring high – precision production and top – notch product quality.
Machine Video
Reviews
There are no reviews yet.